NMB Cooling Fans Deliver Value
Managing heat dissipation and airflow is crucial when designing efficient and reliable electronic devices. MinebeaMitsumi has been manufacturing NMB Cooling Fans for nearly 50 years, and the majority of the components for each fan are produced in-house. This allows us to control each step in the assembly process yielding a more reliable fan that will last. Our engineers continually research new technology for materials, coatings, electronics and more in order to develop cutting edge cooling solutions for our customers. We also have testing equipment located in the US to support our local customers with troubleshooting and custom solutions. Read more about how NMB Cooling fans deliver superior thermal management.
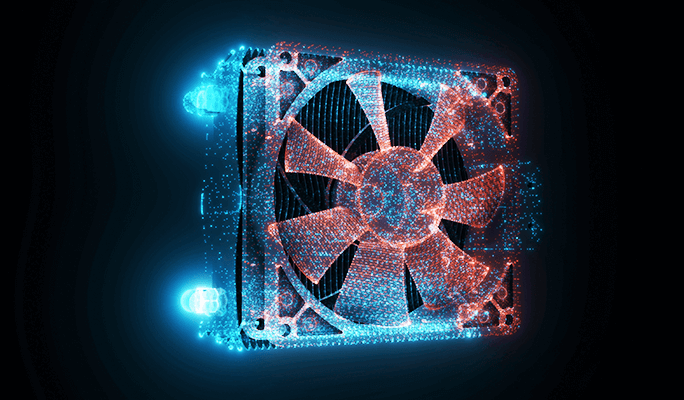
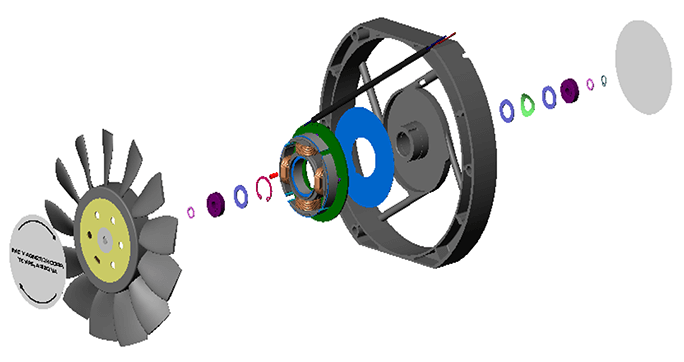
What makes up an NMB fan?
NMB Fans have a reputation in the industry for good reason – they offer great quality and high reliability while remaining cost effective. We accomplish this through a well-established, vertically integrated manufacturing process.
For example, our DC fans are assembled with ball bearings, impellors, stators, casings and shafts that are all produced in-house. In this way, we can better control the materials, parts and testing that go into making each NMB fan which contributes to our industry-leading quality and reliability.
In addition to manufacturing the parts that go into each fan, we also build much of the assembly line equipment and press and stamp machinery ourselves. Through our comprehensive understanding of the production process and advanced cooling technologies, NMB is able to produce the highest quality fans at high volume.
Types of NMB Fans
NMB offers AC and DC axial fans along with centrifugal impellers and blowers. One of the main differences in these products is the direction of airflow generated during operation. Axial fans are so named because they generate air flow in a direction parallel to the axis. This type of fan is ideal for applications that require high air volume, low pressure and an energy efficient design. On the other hand, the movement of air in centrifugal fans is directed outward at an angle perpendicular to the axis. This impeller design is able to produce higher pressure making it suitable for industrial or commercial applications. DC blowers use a similar impeller design but add an enclosed cage that creates a duct or tube. Instead of forcing the air in a general outward direction, this tube projects the air through a single opening creating a concentrated, steady flow of air. Centrifugal DC blowers are typically used in applications with high heat generation and system impedance.
Axial Fan Airflow
Centrifugal Fan Airflow
Centrifugal Blower Airflow
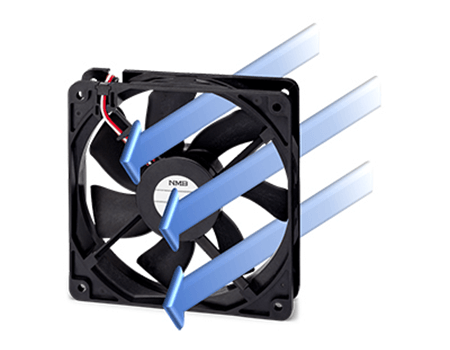
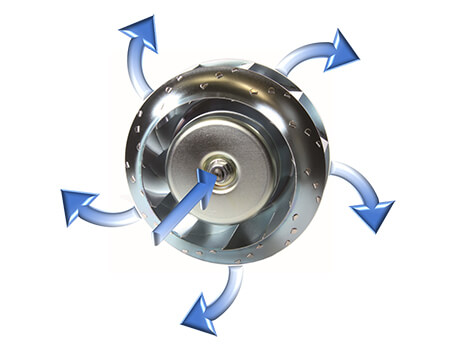
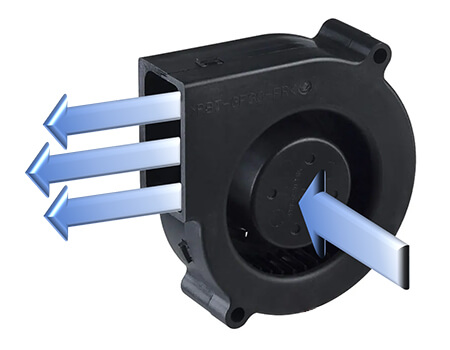
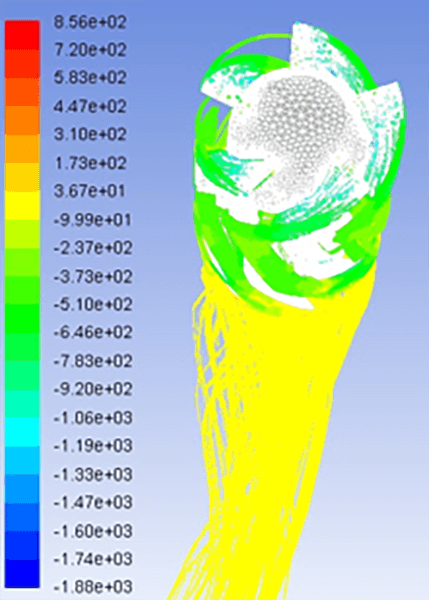
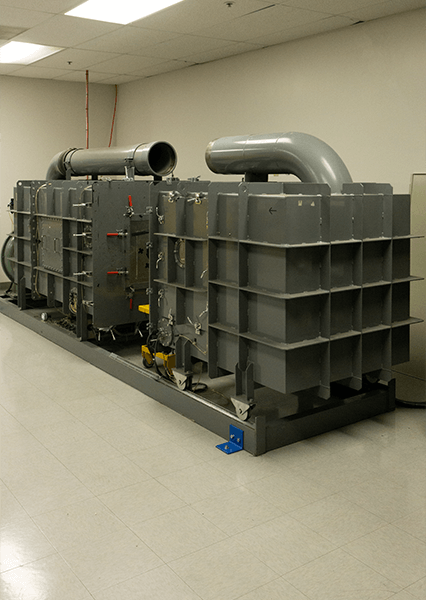
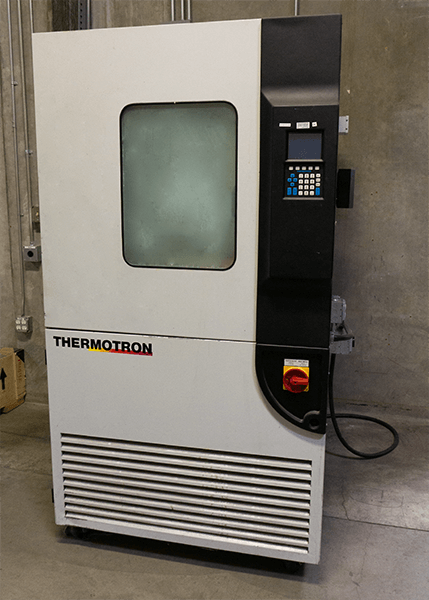
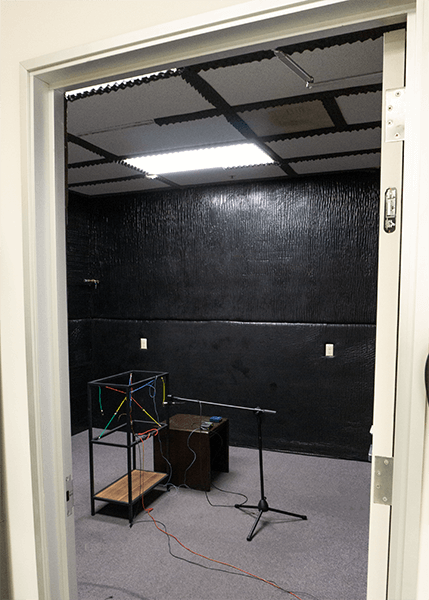
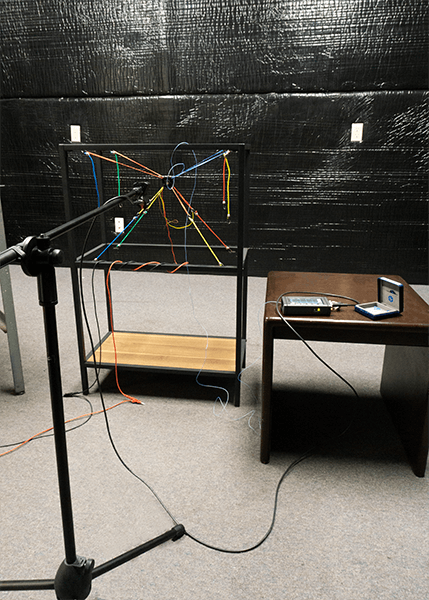
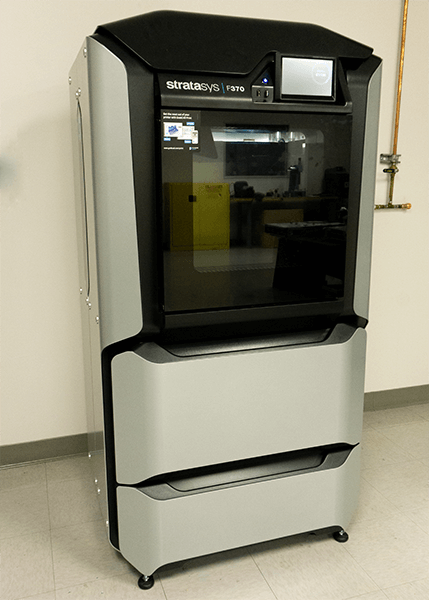
Chatsworth Engineering Center
Local NMB engineering resources can assist with customization and performance analysis in order to optimize cooling for your application. Using state-of-the-art equipment, our support team can analyze air flow, noise, vibration, thermal performance and more. These tools help identify potential issues allowing our team to recommend an ideal thermal management solution to meet your performance needs.
On-site equipment
- Computational Fluid Dynamics (CFD) Simulation – ANSYS FLUENT software allows designers to test products digitally which reduces the time and cost of prototyping. This “virtual test bench” of sorts simulates the flow of air and heat throughout a design.
- PQ Chamber – Fan characteristic curves are generated using a P-Q chamber which measures fan static pressure as it relates to airflow volume. In-house testing equipment makes it possible to evaluate NMB fan performance versus competitors and recommend the best solution.
- Environmental Chamber – The operating environment of a fan is a critical consideration when selecting the right component for your application. We are able to test fan performance at different temperatures to identify a suitable fan for your design.
- Sound Proof Room – Fan noise can contribute to overall satisfaction of the end product. We are able to perform precise noise measurement in-house, and offer suggestions to reduce overall noise (lubrication, materials, etc.)
- Acoustic / Vibration Measurement – Unintentional vibration can negatively effect fan acoustics, performance and lifetime. Through careful analyzation, we can pinpoint balance and misalignment issues and modify designs for the optimal solution.
- 3D Printer – Having access to a 3D printer allows our engineers to rapidly prototype and test different design concepts. Fast turnaround time means we can quickly identify the best fan for your performance requirements.
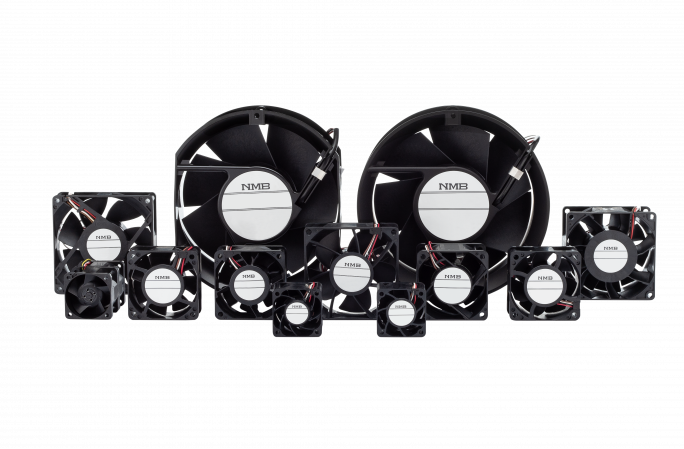
Easily control fan speed with PWM output
NMB DC Fans offer flexible solutions for two, three and four wire fans that can be optimized for your application. In addition to basic open-loop fans, we offer products with Tach Output which provides a feedback that indicates if the fan is running and it’s rate of speed. Our premium 4-wire fans add PWM input to control speed by repeatedly switching the fan on and off according to the duty cycle. In this way, fans can operate more efficiently and remain simple to integrate into various applications.
More custom options for fans:
- Locked rotor output
- Connector type
- Ball bearing (steel; stainless steel; ceramic)
- Lead wire length
- Case surface treatment (metal/plastic; painted/unpainted)
- Potting for ingress protection
Industry leading ingress protection
IP69K-rated cooling fans are the ideal solution for preserving the integrity of electronic equipment in harsh environments. To achieve this designation, the fan motor is fully encapsulated by epoxy material which provides complete protection from dust and high-temperature, high-pressure wash downs. The potting process involves molding and coating, effectively sealing the circuit board, stator and windings with epoxy resin. This process is performed in-house and was developed using our proficiencies in injection molding manufacturing technology. This allows us to surpass IP67, IP68 and even IP69 ratings to achieve the IP69K designation.
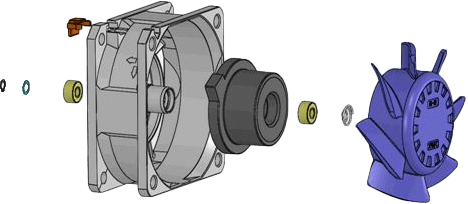
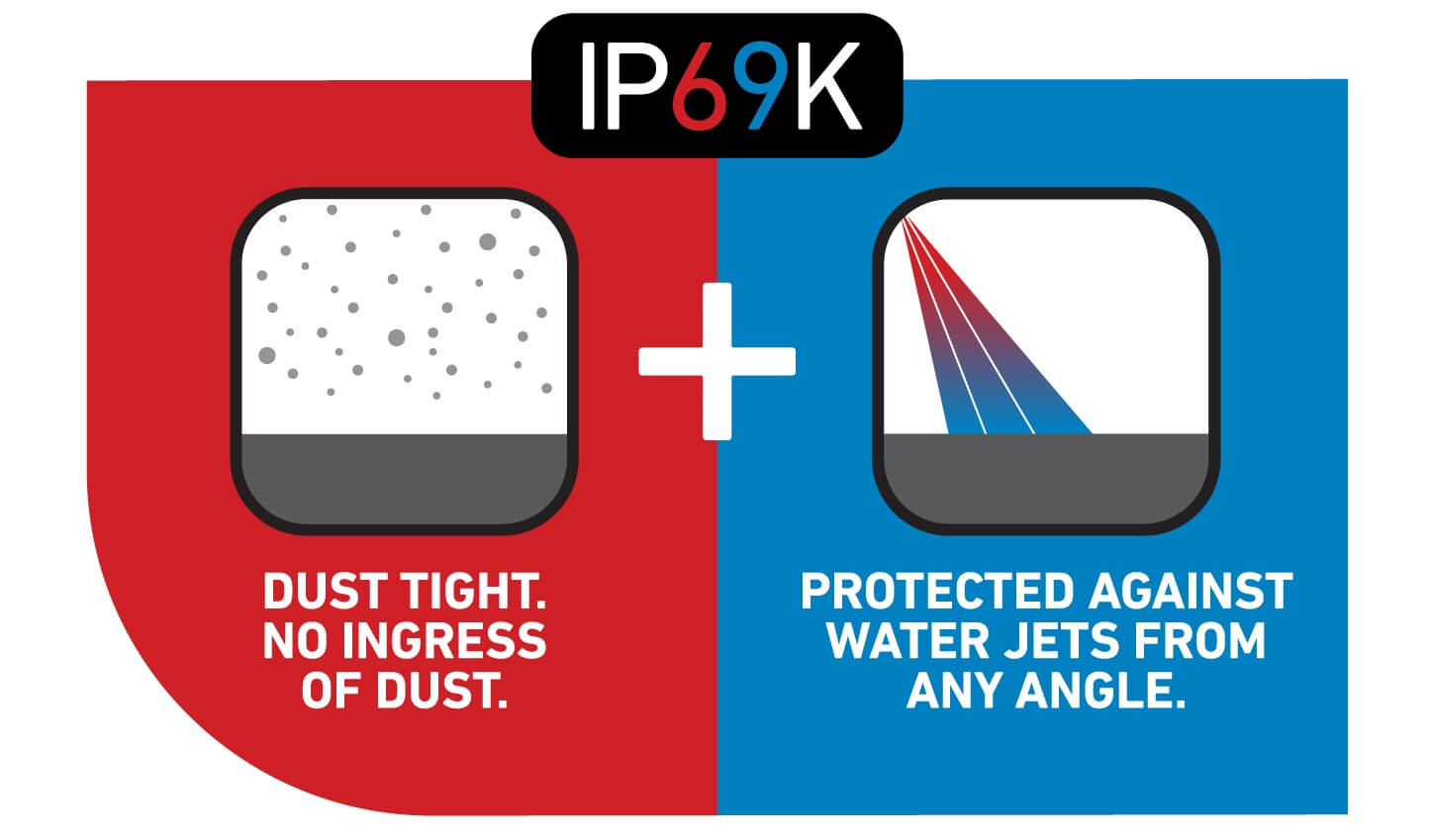
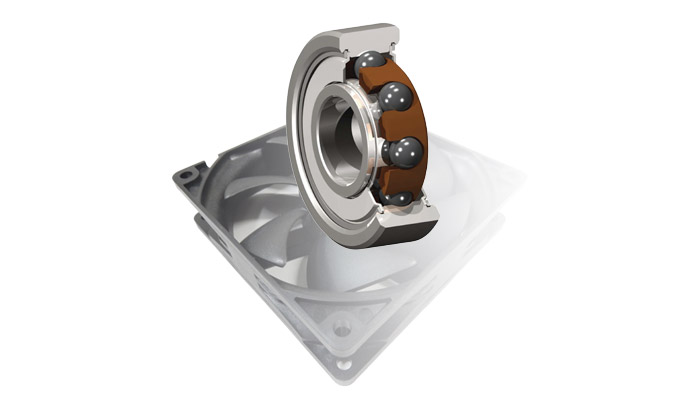
Enhance Fan Performance with Ceramic Ball Bearings
NMB Fans are available with bearings containing ceramic balls on all sizes. Particularly for inverter cooling, we recommend fans with dual ball bearings and ceramic balls to minimize electrical corrosion which can shorten fan life expectancy. Electrical corrosion, also known as galvanic corrosion, occurs when metals contact each other in the presence of an electrolyte. The more noble metal will corrode at a slower rate than the less noble metal. This can cause problems with metal bearings, which are often made of different metals.
NMB bearings with ceramic balls eliminate this problem because they are not susceptible to electrical corrosion. Ceramic balls are made of non-conductive materials such as silicon nitride and do not react with other materials the same way that metals do. To meet longer life requirements, bearings with ceramic balls are preferred. Compared to conventional steel balls, bearing life can be extended when using ceramic balls alongside steel or stainless steel rings. Other benefits include torque reduction due to ceramic balls being lightweight, lower heat generation, and higher operating speed.