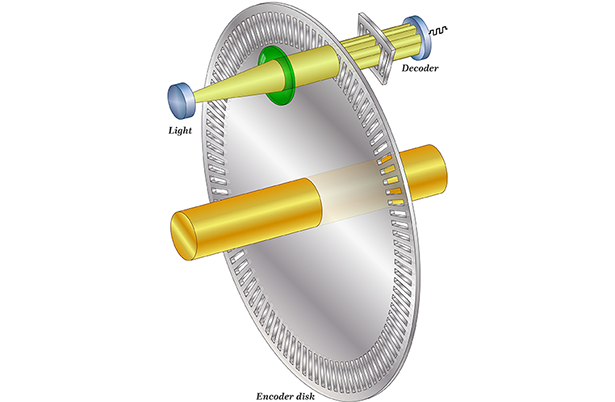
How to Select a Hybrid Motor Position Sensor
Looking around your facility, there’s a good chance that every piece of machinery uses a motor to some degree. Where positioning motion is required, it is likely a stepper motor is employed. However, a stock motor only has an “on/off” switch, with no way of telling where the motor is or how far it’s rotated. This is where hybrid motor position sensors come in.
With a hybrid stepping motor position sensor, you get valuable insight into the position of your stepper motor is, how far it rotated, and how fast it’s going. We offer various types of encoders, each with their own unique features and benefits. In this guide, you’ll learn how to select a hybrid motor position sensor for your specific application, with the help of our expert engineers at NMBTC.
The Importance of Your Hybrid Motor Position Sensors
A stepper motor is designed to move a specific amount, which allows you to achieve specific positions of your motor. However, a typical stepping motor doesn’t have any type of closed-loop feedback, meaning that there’s no telling where the motor is if a stall or misstep occurs.
With a position sensor, you unlock encoder feedback which tells you exactly where your motor is in real time. If a stall occurs, the motor driver can command additional steps or potentially increase current input to overcome stall conditions. Having a high-quality hybrid motor position sensor is imperative in any operation that requires precise motor positioning, especially during applications with higher loads.
The wrong sensor will give you a false sense of security and potentially provide too much or too little data. This can really damage your R&D or production operations.
Hall Sensors
A hall sensor uses magnets that pass over a magnetic array. As your motor’s shaft spins, the magnetic change is calculated by interpolating the signal received. Hall sensors are the most common position sensors on the market, and they’re often used in automation and medical applications.
A hall sensor is great because it can withstand a lot of vibration and shock without failing or giving a false result. Another reason why this sensor is so popular is due to its low cost and simple design — it’s a highly versatile option that will help you position your hybrid stepping motor with very little issue.
The only downside is that this sensor has to sacrifice some resolution quality in exchange for its added durability and simplicity. This sensor doesn’t offer as precise motor positioning data as the others on this list.
Optical Encoders
An optical encoder will track light shining through a premade coded disk, using a photo sensor to see when light is shining through versus when it’s being obstructed. By doing this, an optical encoder can see how much the shaft of your motor moved.
With this ingenious solution, optical encoders offer great resolution, accuracy, and repeatability. They are used in the medical and automation industries to provide cost-effective motor encoding.
The downside with optical encoders is that certain levels of contamination can destroy the effectiveness of the coded disk, causing miscounted steps and incorrect positional data. Like traditional encoders, optical encoders require you to reposition the sensor to “home” and do your recalibration startup sequence if you lose power during an outage, emergency power-off, or machine restart.
Absolute Encoders
Absolute encoders are the newest addition to our sales catalog, and engineers have been saying great things. These encoders are used heavily in the medical and industrial automation industries, and there are countless applications for absolute encoders.
Why are these so popular? One reason is because they don’t need to recalibrate and go “home” after a loss of power or reset. They can pick up where they left off, saving your operation time.
In addition, this encoder style offers “absolute position” — they can give you words and information in real-time as opposed to bit-encoded position output. In other words, your absolute encoder can tell you that your machine is in “pour position” instead of “110”.
Absolute encoders are also more compact, and offer a lot more information. Instead of just counting steps, they can provide velocity and acceleration information.
However, these encoders cost more than traditional encoders. At the same time, they provide a lot more information, so companies tend to save more on their total system cost when they choose absolute encoders.
Resolver Position Sensors
The final sensor style to discuss is resolver position sensors. This sensor style involves an electrical transformer that gets installed at the base of your motor’s shaft. It has a stationary stator and a rotating rotor, filled with copper windings, which works just like a transformer. As your motor spins, the rotor passes through the stator, providing feedback that tells you how far your hybrid stepping motor rotated, and its position in real time.
Thanks to this setup, you’ll achieve the highest level of resolution, up to 200,000 pulse/rev. As an enclosed system, resolver position sensors are also great at withstanding contamination, vibration pressure, and shock.
That’s why you’ll see these sensors used in harsh environments, such as automotive and industrial automation.
Unfortunately, resolver position sensors are more expensive and heavier than other sensors on the market, but their durability and precision more than make up for this.
Conclusion
Picking the right hybrid motor position sensor is the first step to achieving a long-lasting, high-precision, durable positioning system. At NMBTC, we stock a wide variety of hybrid motors with integrated position sensors to ensure you get the best results. Do have specific requirements and need help with selecting a position sensor? Check out our position sensor selection guide for more details. If you need additional assitance, our position sensor experts are here to answer your questions and connect you with the right sensor. Feel free to explore our comprehensive list of hybrid motors with positional sensors and contact us today.