Have a question about this product?

Turbocharger Bearings
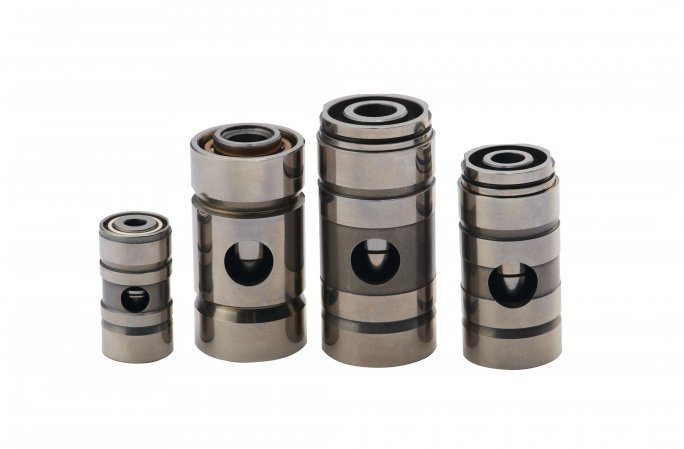
High heat resistant ball bearing units for automotive turbochargers. MinebeaMitsumi has improved combustion efficiency and reduced the time lag between the pedal operation and automobile acceleration by adopting high-heat resistant ball bearings instead of oil-lubricating bearings.
Features:
- Small size
- Low torque
- High durability
- Extreme heat resistance
- Available shaft diameters: 6 mm, 10 mm and 12 mm
- Displacements from 1.4 to 10 L are supported
Turbochargers, in their heyday in the 1980s, were installed in many racing cars and sports cars to enhance the speed and maximum output of the automobiles. In those days, there was a trade-off relationship between the turbocharger and fuel consumption. Recently, a turbocharger has attracted attention once again as a device for boosting the insufficient output of engines that are downsized to meet environmental restrictions. Thus, its arena of applications has been expanded to general automobiles and eco-cars as well.
A turbocharger is a device to increase an engine’s power output with a smaller engine capacity by improving the engine’s combustion efficiency through the recycling of exhaust gases that are normally discarded.
A turbocharger harnesses exhaust gas pressure emitted from the engine cylinder to drive a turbine and a compressor mounted on the same shaft. Air taken in by an automobile is compressed by the compressor and sent to the cylinder, which increases air intake and improves combustion efficiency. The turbine and compressor both play important roles to efficiently send compressed air to the engine. In 2008, MinebeaMitsumi started developing a new type of bearings for a turbine main shaft that directly influences the rotational efficiency.
For years, many turbochargers for general automobiles used oil-lubricating bearings that are highly resistant to harsh environments. These bearings are required to withstand ultra-high speeds of over 200,000 revolutions, while continuously immersed in oil.
However, since the friction resistance of oil-lubricating bearings increases at the time of acceleration and deceleration due to its structure, the speed following capability is inferior to that of ball bearings (particularly when an engine starts at the low temperature). This generates a time lag between the increase in intake air pressure and the step-in operation of the accelerator pedal. Consequently, the driver feels the acceleration to be slow, and depresses the accelerator pedal more than necessary, thereby resulting in poor fuel economy. In actual city driving, since acceleration and deceleration are frequently repeated, a series of those steps tend to affect practical fuel economy.
To address these issues, we had to improve the following four main points for the new type of ball bearing unit: Downsizing along with an engine unit downsizing, high durability, high-heat resistance and low torque. In addition, we had to mass-produce the bearings so that they would be widely adopted for use in general automobiles and eco-cars. MinebeaMitsumi, which has been continuously improving bearing production technologies since its establishment, begun to tackle this challenge.
Compared to oil-lubricating bearings, the structure of high-heat-resistant ball bearings is more complicated. The challenge of durability and heat resistance was solved by combining parts made from different materials. For the inner race and outer race, we adopted M50 bearing steel that is also used for the main bearings of aircraft jet engines; and for balls, we adopted lightweight ceramic materials with low calorific value, suitable for high revolution. We also applied special surface treatment to the retainer to improve the balls’ rotational efficiency. Besides downsizing, unitization allowed us to reduce the assembly work in the turbocharger manufacture and improve the stability and balance of the entire part.
MinebeaMitsumi’s global technical development capability and production system were indispensable for the processes from the development to mass production of the new type ball bearing unit. Our German affiliate, myonic, conducted the basic design and development and another German affiliate, PMDM, worked on the fluid and heat analyses. Then, our Karuizawa Plant carried out the prototype/mass production designing and the Bang Pa-in Plant in Thailand took charge of the mass production. As such, we are able to utilize the comprehensive strength of the MinebeaMitsumi Group.

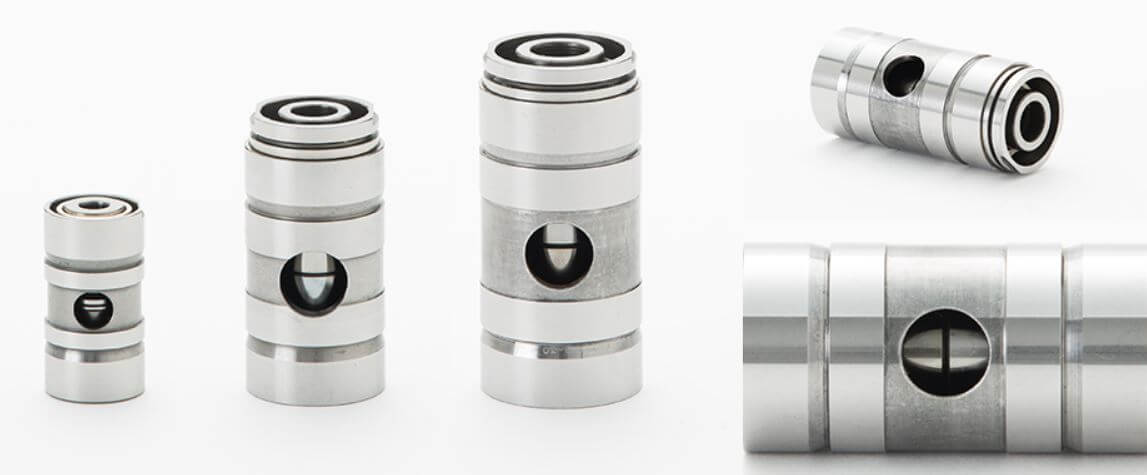
Solutions for Aftermarket Turbocharger Manufacturers
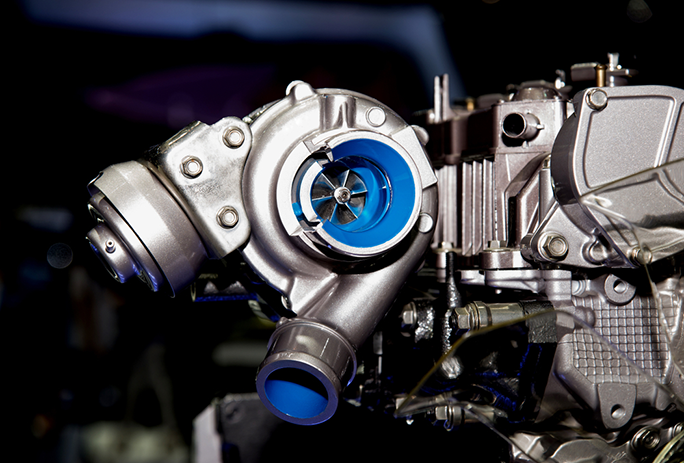
Car enthusiasts are constantly researching ways to enhance their vehicles and optimize the driving experience. Increasing horsepower, boosting torque and improving fuel economy contribute towards advanced vehicle performance. Integrating turbochargers into ICE and hybrid vehicles can deliver better efficiency and reduced emissions.
Model Number |
Inner Diameter (mm) |
Outer Diameter (mm) |
Length (mm) |
---|---|---|---|
AS-1961TP1 |
5.2/6.0 |
18.0 |
34.2 |
AS-1980TP1 |
8.0/8.8 |
22.0 |
42.5 |
AS-1956 |
9.6/10.0 |
29.0 |
62.0 |
AS-1952TP2 |
11.8/12.8 |
38.0 |
55.5 |
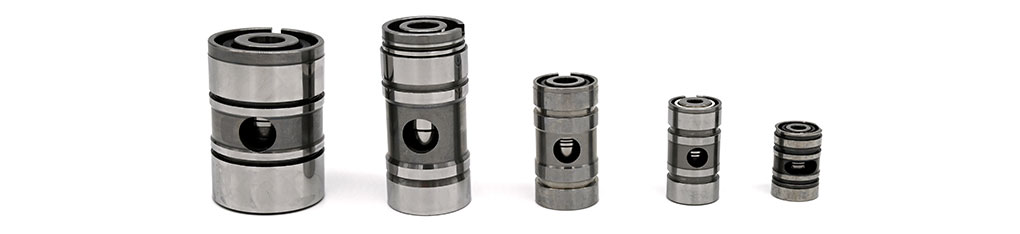