Flanged Bearings and Bearing Types
What makes flanged ball bearings different than other ball bearings? A flanged ball bearing is not truly a different type of bearing. Just as ball bearings are offered sealed or open, they are also available flanged or plain. The flange is just another option given to the design engineer by the bearing manufacturer. A flange is an extension, or a lip, on the outer ring of the bearing, designed to aid the mounting and positioning of a bearing in a delicate or problematic application.
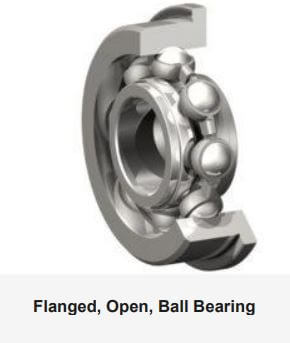
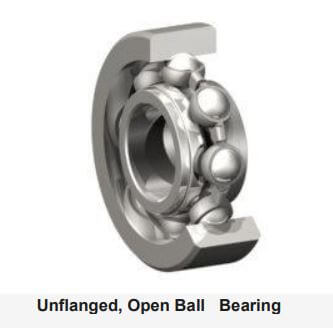
Why are these types of bearings needed?
Flanged bearings are most commonly used when the application requires the bearing to be locked in place. The design engineer will want to lock the bearing axially, along the shaft, or perpendicular to the shaft, radially, depending on his application. A flanged bearing is used in this instance to help withstand axial thrusting. If there is any axial load or axial push on the bearing, the flange will prevent the bearing from moving axially.
What applications benefit from these types of ball bearings?
Any application that will require a bearing to be mounted in a high vibration area, as well as any application that requires high axial loads, will benefit from using a flanged bearing. Automotive applications are a good example; all vehicle components must be able to withstand high vibrations. The design engineer needs to be able to select and assemble a bearing that will withstand vibrations, as well as high temperatures. Therefore, adhesive or interference fit in the assembly of a bearing into an automotive application is often insufficient. In order to insure long life and durability of the bearing, the selection comes down to a flanged bearing. A flanged bearing will maintain its position and will survive the hostile environment and vibration within the vehicle. If necessary, assembly of a flanged bearing can also include a secondary attachment, like a retaining clip.
Very high temperatures will also require the selection of a flanged bearing. Under the hood applications, where temperatures are often around 180°C and the presence of materials such as those between a ball bearing and a housing or shaft, it will create a different rate of thermal expansion.
For example, a steel bearing is pressed into aluminum housing; the housing may expand earlier than the steel bearing thus losing the interference with the bearing. The use of a flanged bearing in this application will hold the bearing in place axially – regardless of the imbalance in the expansion rate.
Flanged bearings are most commonly used in light-duty applications, such as food processing machinery, conveyors, material handling, belt drives in HVAC, textile machines, baggage systems, medical processing and various other light-duty industrial applications.
How are these bearings installed?
Once the decision has been made that a flanged bearing is necessary for the application, then the installation of the bearing is not complicated. The drawback is that many types of flanges are expensive to manufacture, and will increase the cost of the application design.
Closing recommendations
In closing, keep in mind that it’s rare to encounter an application where a flanged miniature ball bearing is required. It is important for the design engineer to discuss all application alternatives with their bearing supplier because there is a cost increase by selecting a flanged bearing. The design engineer needs to make sure that he is not over-designing the application in relation to the need for a flanged bearing. He may find that there are often less expensive options available for bearing control. However, for some applications, flanged bearings are the only good alternative. Therefore, definitely talk to an expert to be sure before making a final decision.
Different Types of Ball Bearings
Angular Contact Ball Bearings
Bearings that are angular contact ball bearings have a contact angle, which means the force is applied away one raceway to the other particular angle. This makes this type of bearing suitable for combined loads, which have a high axial force and transfer of energy with radial forces.
Self Aligning Ball Bearings
Self-aligning ball bearings have a doubled row of balls that are guided by a cage with a double row inner raceway. This type of bearings also has a unique feature: a spherical outer raceway that complements the rest of the bearing with a swivel, allowing for the self-alignment capabilities of the bearing.
Roller Bearings
Roller bearings are most noted for having line contact. Line contact allows for a higher load rating than a regular ball bearing of the same mass or width. However, there will be more friction and these bearings are more suited for slower speeds.
Spherical Roller Bearings
Some of the strongest bearings are spherical roller bearings, using spherical rollers instead of ball rollers. This allows for higher loads and can cover for any problems between a shaft and housing makeup. These bearings also work well with high to moderate radial loads.
Thrust Ball Bearings
Thrust ball bearings are made up of two bearing discs with raceways as the balls within the bearing. These were developed this way for absorbing axial forces, meaning they can move along the shaft axially in only one direction.
Deep Groove Ball Bearings
These are the most common types of ball bearings. Deep groove ball bearings are simple and easy to take care of, they wear out slowly and can work in most environments easily. They have low torque and can work at high speeds.
Cylindrical Roller Bearings
Cylindrical roller bearings keep contact along a line between the rolling elements of the bearing and the raceways. This makes the most efficient usage of stress factors from the point of contact, meaning cylindrical roller bearings have a very high radial load rating, and the ability to transmit axial load.
Needle Roller Bearings
Needle roller bearings are a very specialized type of cylindrical ball bearing, containing thing long rolling elements which are called needle rollers. They usually have a very low ratio of diameter to length, and they have a high load capacity making them work well with high radial forces.
Tapered Roller Bearings
Tapered roller bearings have a tapered raceway in the outer and inner rings, which have conical rollers between them. With the contact angle, tapered roller bearings can withstand high radial and axial forces in a single direction. Pairs of tapered roller bearings are often employed together to support axial force in both directions.
(Original Content for Design World – Bearing Tips
Joyce Laird – Contributing Editor interviewing Dave Nufer – NMB Sales Engineer for Turbo, Specialty & Ball Bearings )